Predictive Maintenance for Wind Turbines
- Christian Fontius
- Jan 27, 2022
- 4 min read
Updated: May 26
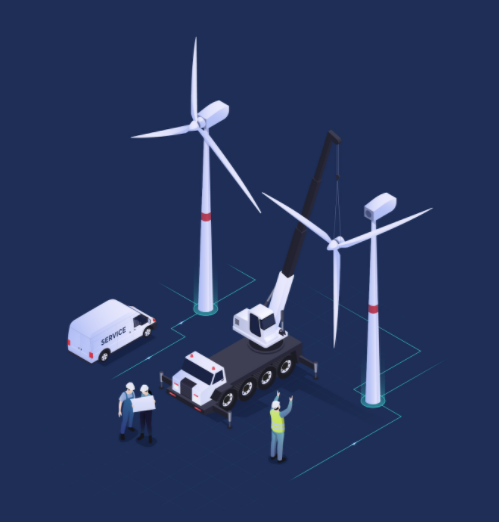
For all the hope that lies in them, wind turbines (WTGs) bring challenges that demand urgent solutions.
1. High maintenance costs: Up to 30% of levelized costs per kWh generated during the lifetime of a wind turbine can be attributed to operation and maintenance.
2.Downtime: Turbine failure can easily result in downtime of a week or more – resulting in respective downtime costs.
3.Tricky and time-intensive repairs: Transporting spare parts is expensive and, depending on location, not without difficulty. Transportation often takes more time than the repair itself. It is estimated that over 70% of WTG downtime comes from unplanned repairs.
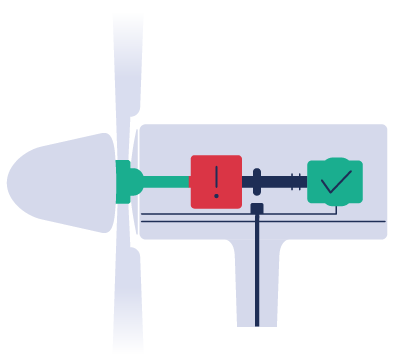
Early defect detection, maintenance and repair optimization, and downtime prevention are therefore key factors in achieving a positive return on investment for wind turbines.
But how can wind farm operators reliably detect damages at an early stage?
The Solution: Predictive Maintenance Through Artificial Intelligence
Since in-depth information on Predictive Maintenance (PdM) in wind power is hard to come by, we decided to cover the following points in this article:
- Scope and opportunities of artificial intelligence (AI) in PdM
- Potential use cases of AI-based PdM
- Benefits of for owners
You’re looking for some real-life examples? We share four case studies from our everyday work in this whitepaper:
Definition of Predictive Maintenance for Wind Turbines
Predictive maintenance includes a series of activities that detect changes in the physical condition of components (signs of failure) to enable timely maintenance activities, maximize component life, and reduce downtime.
Predictive maintenance thus aims to achieve three goals:
Longer runtime of wind turbines in normal operation, limiting abnormal behavior, and minimizing downtime
Prevention of expensive major incidents, extending the service life of individual components through taking early action
Monitoring of repair measures and success rate tracking
The Challenge of Predictive Maintenance in Practice
Every wind turbine behaves differently. However, these differences aren’t usually considered in predictive maintenance analyses.
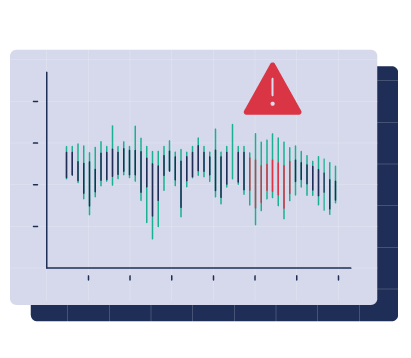
Example: Let’s assume a manufacturer sets the static limit of a rotor at 50°. That limit may not be reached in winter, even though the component is overheating – compared to its normal and expected behavior. The warning signal will go unnoticed when external factors (such as weather) aren’t considered in an analysis.
The factors that influence individual WTG behavior include:
Location - i.e. turbulence, shading, local weather - influences, among other things, the individual behavior of a WTG. This results in different component wear states.
Installed components: Over the lifetime of older turbines particularly, varying components may be installed to reduce repair costs. Sensors can therefore be installed in different places. Additionally, different lubricants and oils affect temperature behavior.
Various data interfaces, data formats and controls being used.

That’s why sensor data tends to not get monitored properly in day-to-day operations (apart from basic performance monitoring). Current asset management software neither evaluates the data nor is the data logged, depending on the provider. Meaningful information can hardly be derived from missing or non-uniform data sets using simple statistical methods. As a result, small damages along the drive train can grow to major incidents over the years.
Artificial intelligence learns the normal behavior of each wind turbine and triggers alarms in case of deviations
Sensor data reflect the physical reality each individual WTG at any given time. And neural networks make sense of this data:
Neural networks learn each WTG behavior individually over the course of the year and determine what normal behavior looks like. They then match data measurements with predicted behavior. Detection algorithms can thus find anomalies - i.e. deviations between real and simulated behavior - at an early stage, enabling rapid action and preventing major incident to the main components.
This is what the process for learning normal behavior per WTG, component, and for detecting anomalies looks like:

Use Cases of AI-Based Predictive Maintenance
At Turbit, we have long been using AI for predictive maintenance as well as performance optimization of wind farms. So, the following findings are drawn from our many years of practical experience. Neural networks pull their information from the following data points:
- SCADA data
- Logbooks
- Maintenance reports
- Software updates
- LiDAR data
- CMS data
Good data quality allow us to detect changes in the behavior of all major components as well as adjacent subsystems. Here’s an example from one of our customers.
How We Detected Damage to the Main Shaft at an Early Stage
In October 2021, Turbit sent an alarm due to excessive temperatures in the main bearing. After on-site inspection, it was deemed necessary to replace the main bearing.
In January of 2022 the main bearing was exchanged. The customer was able to plan this repair by crane several months in advance. Early detection reduced costs since this type of damage often leads to main component damage or downtime of several weeks – which the customer avoided.
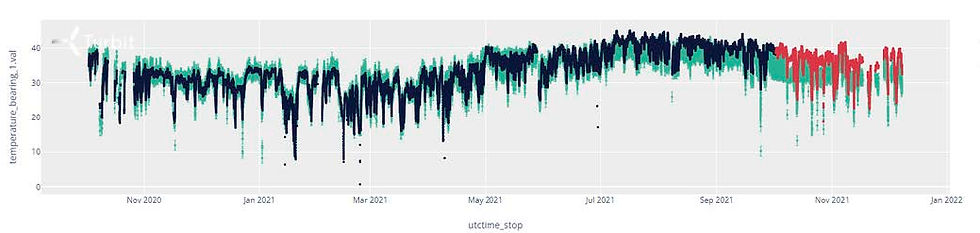

An excerpt of further damages detected by Turbit:
- Diagnosis of a run-in generator
- Detection of a defective crimp joint in the corrugated tube
- Measurement of increased temperatures in the generator bearing
- Clogged air filters
- Leaking oil rings
- Overheating pitch motors
You can find a detailed overview including visualized data in our whitepaper on the topic.
Conclusion: Advantages of AI-Based Predictive Maintenance for Wind Farm Operators
Neural networks learn the normal behaviour of each wind turbine and simulate expected future behaviour. Simulated behaviour is then compared to actual real-time data. That’s what makes reliable early detection of abnormal behaviour for each turbine type possible.
Early detection of changes in the physical condition of components leads to three main benefits:
Prevention of major incidents
Reduced downtime
Extended component lifetime
When you can plan repairs in advance and thus group them together, you can reduce travel and transportation costs for spare parts. And the key to good AI monitoring is a high quality dataset.
Is your SCADA data any good?
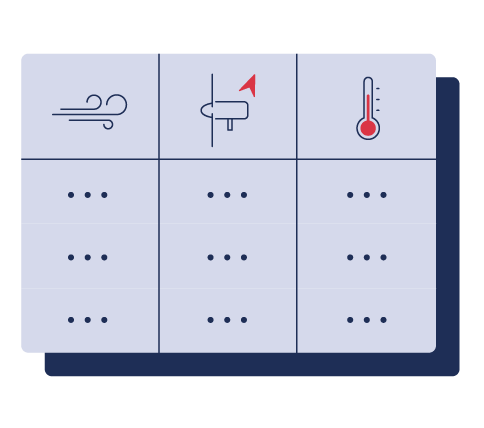
The first step on your way to predictive maintenance is a data check to evaluate your data quality. For an initial assessment, you just need a simple SCADA extract from your operations management system.
Send us an email including a short SCADA extract (one week) to datacheck@turbit.de
We'll reply with an assessment of AI Monitoring options based on your data.
Comments